|
continuous
dyeing carpet
Continuous Dyeing Carpet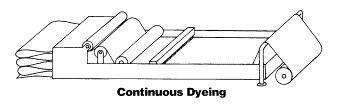
Continuous dyeing carpet method is used for solid-color cut-pile carpet.
Continuous dyeing is one of the fastest, most cost-effective means of
color application. Long expanses of tufted carpet travel through huge
machinery to be wet and scoured. After some of the water is extracted,
the carpet moves under a dye applicator that flows dye liquor onto it at
a rate of 50' per minute. Next, the carpet is put into a wet heat
steamer to fix the dye, after which it is washed, extracted, and dried.
The majority of the continuous dyed carpet equipment used in the world today is manufactured
by two companies in Gemany, Kusters and Fleissner. This type of continuous dyeing method is
favored over beck dyeing due to the fact that costs are lower for utilities,
labor, and raw materials. The reason for this is that beck dyeing
requires more water, about 6 times more water in fact, for processing
the same number of pounds of dyed fiber as compared to a continuous
dyeing line. The need for more water brings the need for more energy to
heat the water, and more chemistry to treat the water and carpet fibers
adequately for the dyeing process.
A beck produces one 1800 lb dyeload in about three hours, giving a 600 lb/hr output for dyed
carpet. A beck operation generally consists of about ten becks and a dryer, with a
crewing of roughly twelve people, with an output of about 6000 lb per
hour of dyed carpet. This beck dyeing operation will require about
43,000 gallons of water per hour to operate. A modern continuous dye
line can be designed to operate at a speed of 90 feet per minute on 32
oz per yard carpet, this gives an output rate of 14,000 lb per hour of
dyed carpet. This line would be manned by about ten people, and would
consume about 10,000 gallons per hour of water. As you can see, the
continuous dyeing line has a far greater output of dyed carpet with fewer
people and a much reduced water demand.
In the past, the main downside of this dyeing
method was sidematch control. The beck dyeing process,
although more expensive and more water demanding, produced overall
better sidematch control as compared to continuous dyeing. Advances in
control systems for the this process have improved the
sidematch control to the point that, today, we can say, that dyeing in
this manner offers equal sidematch control as compared to becks, along with
the environmental and cost advantages previously mentioned.
See Also:
skein dyeing |
space
dyeing |
solution
dyeing
©2010 FloorBiz, Inc. All Rights Reserved
Flooring |
Flooring Guide |
Flooring Info |
Flooring Forum
| |